The science of printing currency
Money is nothing more than a medium of exchange. For hundreds of years paper currency has reigned supreme – our ancestors didn’t have to lug around gold coins when they wanted to buy goods and services (more money really did mean more problems!). Paper currency began when individuals brought gold to a bank where their coins would be stored in exchange for a paper receipt that was a promissory note to repay the gold coins. Needless to say, it was easier to carry a receipt than carry the gold. Money has always been a common denominator that allows us to exchange the skills we perform now, into something that society perceives as valuable, in order to redeem it at a later time.
Paper currency is a fascinating topic because it’s something we interact with on a daily basis, but we don’t typically give a lot of thought to the printing processes behind the notes. As the printing technology to manufacture currency becomes more advanced, so does the technology for those trying to manufacture counterfeit currency.
Printing Lines & technique
dns-secure procured the latest currency printing banknote fabrication lines directly from the international manufacturing companies. Combination of European, Japanese and other international companies by capacities of 800 million production banknote per year. Each currency printing line made up of some stages of different technology concerning of security printing which coming out of complexity while will be comments in general /public usage .
All kinds and types of printing processes can be used in printing all kinds of security documents and prints. Offset, flexo, intaglio, screen, digital and relief printing processes can be used separately or integrated together in printing the secured prints and documents. Using more than one printing technology in printing security documents, like in the case of banknote printing, makes it very difficult for the forgeries to try to counterfeit them.
Another important is a technique called Rainbow printing, where the same ink fountain is divided by special dividers and splitters, in order to use several inks with different colors in the same ink fountain, producing very special color mixes blends and shades, that are very difficult to reproduce.
Also using special numbering during the printing process is very useful specially using different sized horizontal and vertical numbers.
Modular Systems
Modular Systems are designed to integrate seamlessly, ensuring production environments can evolve to meet future demands – without unnecessary expenditure. This helps keep costs to a minimum.
We are proud of our reputation for production reliability. But when things do not go as planned, innovative design features enable simple system access, easy maintenance, and less downtime.
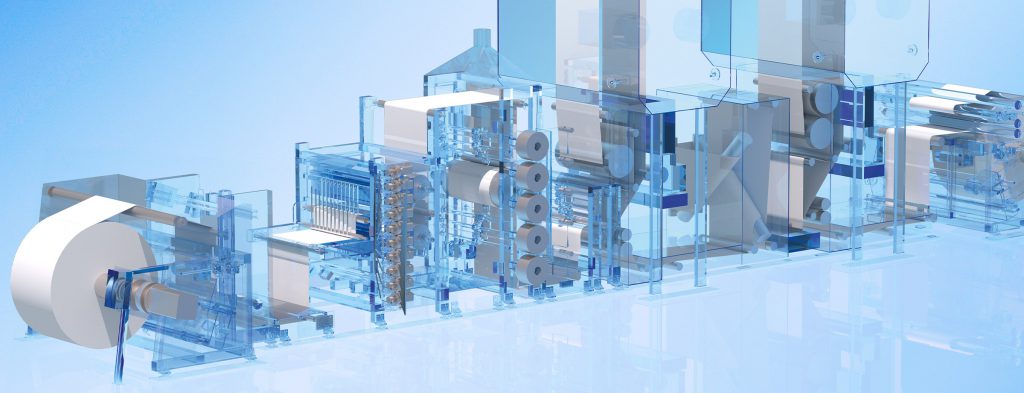
Offset lithography is a multi-step process that uses etched metal plates, water-repellent (e.g. oil-based) inks, water, blanket cylinders, and impression cylinders.
The plates are created so that oily inks adhere only to the portions of the plate that contain the images and text. A thin film of water over the blank areas of the plate repels the oil-based inks.
The ink on the plates is first transferred to a rubber-wrapped “blanket” cylinder. The ink reaches the paper when the inked blanket cylinder rolls over the paper.
Many presses used impression cylinders to apply pressure to the paper as the ink is being applied to the paper surface. Impression cylinders also help move the sheets through the presses.
The offset printing process requires making separate plates and blanket rollers for each color of ink that will be used.
Different variations of presses, plates, and inks are used for different run lengths and substrate requirements. For example, some presses may print in roll processing system . Other presses may print small to large sheets that will be used in different applications even security purpose and banknote .
Rainbow Offset Printers:
in security purpose of offset technology generally use of additional technique to add security to documents , in Rainbow technique a security background pattern shall be designed to be resistant to counterfeit by scanning, printing or copying, with multicolored security inks and positive and negative guilloche printing; the pattern shall not be composed of the primary co-lours (CMYK), shall contain complex pattern designs in a minimum of two special co-lours and shall include micro lettering
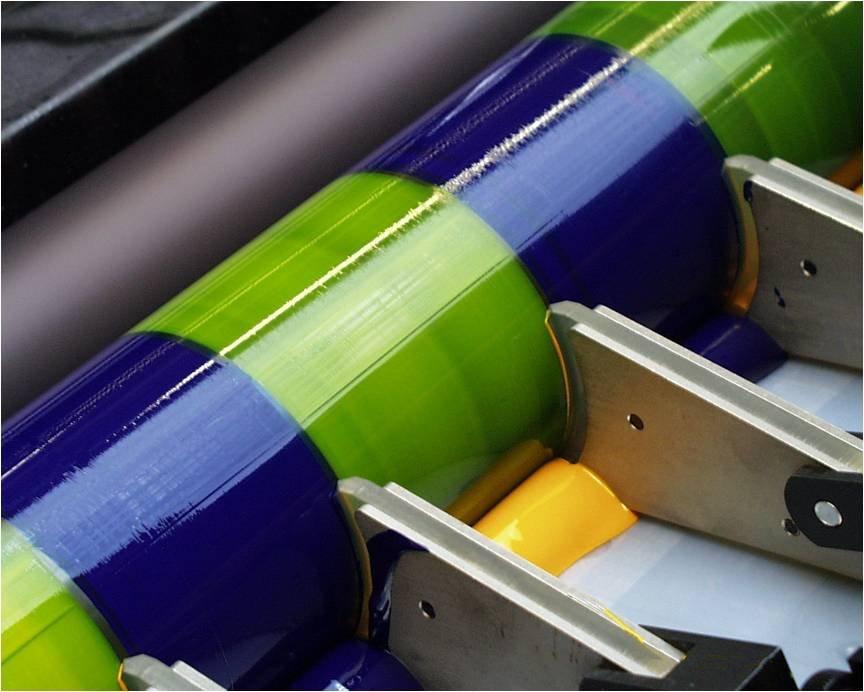
Screen printing is especially suitable for the application of thick ink films on banknotes, particularly optically variable and iridescent inks. The inks are highly valuable so it is imperative they are applied in the most efficient way.
Optically Variable Devices (OVDs) are used on many banknotes in circulation and can be applied in the paper mill or the print works. In order to reduce waste and increase security by under-printing and overprinting, the print work is the place of choice.
Optically Variable Image Devices (DOVID):
These are coatings and laminates, transparent or opaque, which are added on the surface of the prints (in some non-paper materials, like plastics, they can be embedded within the different layers), to add some more security elements, helping in deterring counterfeiting. These devices are characterized by having different appearances (content, color or info), when viewed at different viewing or lighting angles.
Samples of these kinds of devices are holograms, Kine-grams. Iridescent optically variable coatings are also sometimes classified under the same title or as OVDs (Optically Variable Devices).
In conclusion, we’d like to use Richard Warner’s and Richard Adams’ words from their book “Introduction to Security Printing” published by GATF in the USA: “One of the most widely agreed-upon practices used by security printers to mitigate counterfeiting attempts is to use several security printing devices on a given document, and to replace these devices with new and/or different security devices with regularity.” And Gordon’s words, that the goal of today’s security printer is to produce documents with multiple layers of new counterfeit deterrents while maintaining the aesthetics and functionality of the printed product.
The latest generation of Intaglio presses creates savings of up to 15% in ink consumption, while at the same time, wiping solution’s recycling system dramatically reduces environmental impact.
The Future of Intaglio Summit represents a coming together of industry decision-makers, designers, engravers and other stakeholders in the banknote design and issuing process. Our goal is to facilitate an open exchange and dialogue on what the future of intaglio should and could look like and what steps need to be taken by our industry to get there.
Why Hold a Summit?
Intaglio has served the banknote industry for over 100 years but despite its multiple qualities and virtues, this industry appears uncertain about how to fully utilize this technique in modern banknote design. Clearly some degree of consensus and a unifying strategy is required to enable the banknote industry position this unique printing process alongside the growing number of security technologies available. Intaglio is at cross-roads and in order to determine the best way forward all actors and stakeholders in the banknote development, issue and user chain must come together and begin communication.
The Future of Intaglio Summit has been developed for this very reason – to facilitate open exchange, dialogue and sharing of information to support a more sustainable and long-term strategy to managing intaglio for the benefit of the banknote industry in the future.
The Issues:
Intaglio is a true multi-dimensional technique contributing to a wide range of defining banknote assets including:
- Recognition (User Experience)
- Durability
- Security
- Machine-readability
- Integration
- Design
However, a growing number of diverse opinions concerning the cost, time, resources, technology and quality have been fueling the need to re-examine the value proposition represented by intaglio in today’s world. The Future of Intaglio Summit will address these issues head-on via a series of presentations and panel discussions and attempt to bring together a common and more informed consensus on how to best use intaglio in the future, establish a clear set of measurable goals and define what measures need to be taken to achieve these.
A Global Perspective:
To ensure that we can consider the perspective of all actors and stakeholders who have an interest in the intaglio development and deployment chain, the Future of Intaglio Summit will be preceded by a series of global surveys designed to reach and gather information from the international central bank, printer, designer and cash-cycle communities/ industries. This exercise will allow us create an up to date and accurate picture of the current and future expectations from intaglio as a technique/feature and intaglio as a process.
The Main Subjects Addressed Include:
Intaglio Content:
- More vs. Less
- Simplicity vs. Complexity
- Bigger vs. Smaller Portraits
- Intaglio Level 1 Tech Integration
- Text & Key symbols
Intaglio Value
- The User Experience
- Machine Readability
- Durability & Substrates
- Security
Intaglio Challenges
- Quality vs. Commodity
- Intaglio Engraver vs. Intaglio Designer
- Design Tools & Technology
- Origination Process
Intaglio Trade-offs
- Intaglio Cost vs. Value
- Intaglio Cost vs. Quality
- Intaglio Quality vs. Time
- Intaglio Recto Verso
The use of smart numbering boxes dramatically increases the efficiency of the process. The integration of full-sheet inspection, numbering and varnishing, reduces the needs for labour, storage and space.
Printing the colored Treasury seal and serial numbers
- After the intaglio printing process, the stacks are cut into sheets and are visually examined for defects. Each sheet is fed into a letterpress which prints the colored Treasury seal and serial numbers on the face of the bills. usually the sixteen serial numbers are printed at the same time. The press then automatically advances the numbers before the next sheet of sixteen is printed. The numbers on any sheet are separated.
- The finished sheets are inspected with machine sensors, and any printing errors, folded paper, inclusion of foreign objects, or other defects are identified. Any bills which are found to be defective are marked for later removal. Such bills are replaced with star notes which are numbered in a different sequence and have a star printed after the serial number.
Providing the means to finish, cut and package banknotes through the integration of powerful technology in a seamless workflow.